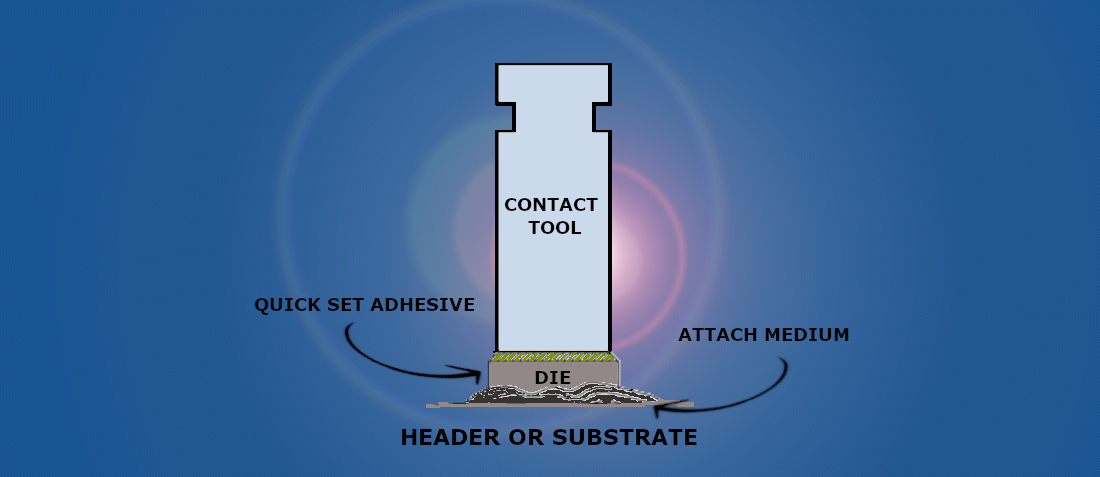
DC power – Use of Substrate Attach Strength – Die Shear Strength Method
- Posted by José Cándido Vázquez Cárdeno
- On February 13, 2019
- 0
The purpose of the test is to determine the strength of the element attachment system when subjected to force in the Y1 axis, and thus to determine the integrity of materials and processes used to attach semiconductor die or surface mounted elements to package headers or other substrates. The implementation of this test includes material evaluation and process control.
Development, volume, and weight of such power units and power rails contribute to the costs of space missions. At the same time, the power distribution to the modules with low voltages and high currents requires heavy power rails due to large cross-sections or suffers from conduction losses or both.
DC power
As DC power is supplied to extended distances from the source, the system bus power is delivered at a much higher bus voltage in order to reduce weight and resistive power loss. System source voltages are commonly a nominal 12V, 28V, 48V, 120V and in some cases 270V.
Power conversion is typically accomplished in multiple stages to reach the final load voltage. Isolation and regulation are two key requirements and may be implemented at different stages depending on system architecture. Although power is lost at each conversion step, it is not practical to deliver the lowest voltages over significant distances due to the high currents and consequent high resistive losses which would be incurred. Designers must balance the advantages and disadvantages of multi-stage power conversion, the tradeoffs of distance, and the need for intermediate voltages to power other circuit elements that often drive the architecture.
The multitude of low-voltage, high current loads and increased system power efficiency requirements make yesterday’s typical design approaches less practical, and design requirements more difficult to achieve.
Traditionally, there are at least two basic design approaches for most power design solutions.
One common solution is a decentralized approach where several isolated DC-DC converters operating directly a space craft power bus (or just one with several outputs), which provide the regulated supply voltages, 1V, 1.5V, 2.5V, 3.3V, 5V, etc., as required by the digital loads.
Get a quick price/delivery estimation of your components, being the first in front of your customer
- Radiographic Inspection 3D X-Ray – 2D - September 14, 2020
- SOLAR CELLS - February 24, 2020
- DC power – Use of Substrate Attach Strength – Die Shear Strength Method - February 13, 2019
0 comments on DC power – Use of Substrate Attach Strength – Die Shear Strength Method